БМД из стеклопластика и керамики — в СССР предлагалось и такое
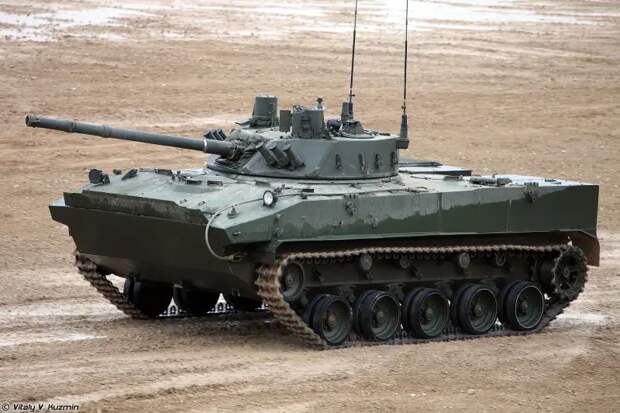
Как известно, комбинированное бронирование, предусматривающее применение различных металлических и неметаллических элементов в защитных структурах, активно использовалось при создании целого ряда советских основных танков, начиная от Т-64 и заканчивая Т-80.
Чего, в общем-то, нельзя сказать о серийных машинах куда более лёгкого класса — БМД и БМП, чья броня, во многом по технологическим причинам, всегда ограничивалась сталью и алюминием (по отдельности либо в сочетании).Однако не стоит думать, что разработка комбинированной брони для лёгкой бронетехники в СССР не велась совсем — проекты и предложения по этой теме были, причём некоторые из них выглядели весьма интересно. Примером может служить броня из стеклопластика и керамики для БМД, подробное описание которой было опубликовано в 1990 году. Его мы и предлагаем к прочтению, поскольку пересказывать слова авторов нет никакого смысла, если есть возможность ознакомиться с оригиналом.
Использование композитных материалов для лёгких ВГМ
В последние годы в нашей стране и за рубежом «доводятся» опытно-конструкторские работы по применению композитных материалов для ВГМ. Из зарубежных работ наиболее известны попытки создания корпусов из композитных материалов американских БТР и БМП. Их целью являлось снижение массы машин при сохранении заданного уровня броневой защиты.
В СССР исследована возможность создания корпуса из композитных материалов для боевой машины десанта (БМД), корпус которой изготовлен из броневых материалов на основе алюминиевых сплавов. Для этой машины была предложена конструкция корпуса на основе стеклопластика и керамики. Было установлено, что для корпуса БМД с защитными модулями из стеклопластика толщиной 15 мм и керамики толщиной 8 мм при сохранении массы алюминиевого корпуса можно обеспечить полную защиту от 7,62-мм бронебойной пули со всех дистанций. При этом выигрыш в массе – по 32 кг с каждого квадратного метра поверхности корпуса. На макете такого корпуса был достигнут 25%-ный выигрыш в массе при одновременном снижении поражаемости бортовых проекций бронебойной 7,62-мм пулей с дистанции от 500 м до 0. Оказалось, что энергозатраты на производство корпуса из алюминия в 1,5 раза, а корпуса из композитного материала вдвое меньше, чем на производство стального корпуса.
Результаты натурных испытаний обстрелом различных конструкций преград на основе стеклопластика с керамикой (рис. 1) показали, что их применение для защиты от бронебойных пуль может обеспечить выигрыш по массе до 50% по сравнению с равностойкой стальной броней. Использование этих результатов и опыта изготовления макета композитного корпуса позволило перейти к разработке конструкции, технологических процессов и изготовлению экспериментальных образцов корпуса БМД. При проектировании корпуса необходимо было обеспечить полную идентичность его внутренних объемов алюминиевому образцу корпуса, сохранить наружные обводы для установки серийного наружного оборудования, гидропневматической подвески и др. Для корпуса машины из стеклопластика был разработан метод контактного формования. В основу технологического процесса изготовления экспериментального корпуса БМД положена технология, применяемая в судостроении.
Для стеклопластиковых элементов конструкций использована стеклоткань марки Т-11-ГВС-9 по ГОСТ 19170—73, а в качестве связующего — смола марки ПН-609-21М по ОСТ 6-05-431—78. Формование стеклопластиковых элементов и конструкций выполнено из расчета 22 слоя стеклоткани на 10 мм толщины. При формовании фланцев и набора соблюдены конструкторские требования к их толщинам без учета числа слоев стеклоткани, но не менее 22 слоев на 10 мм. Формовать наружную оболочку можно, используя единую (разбираемую) модель. В этом случае изготовленный корпус получается в виде единой неразборной детали. Серьезным недостатком данного метода являются невозможность изготовления качественной наружной поверхности, а также трудности установки наполнителя при формировании корпуса. Для повышения качества изготовления корпуса применено формирование его отдельных деталей (днища с бортами, крыши) в матрицах с последующей сваркой деталей.
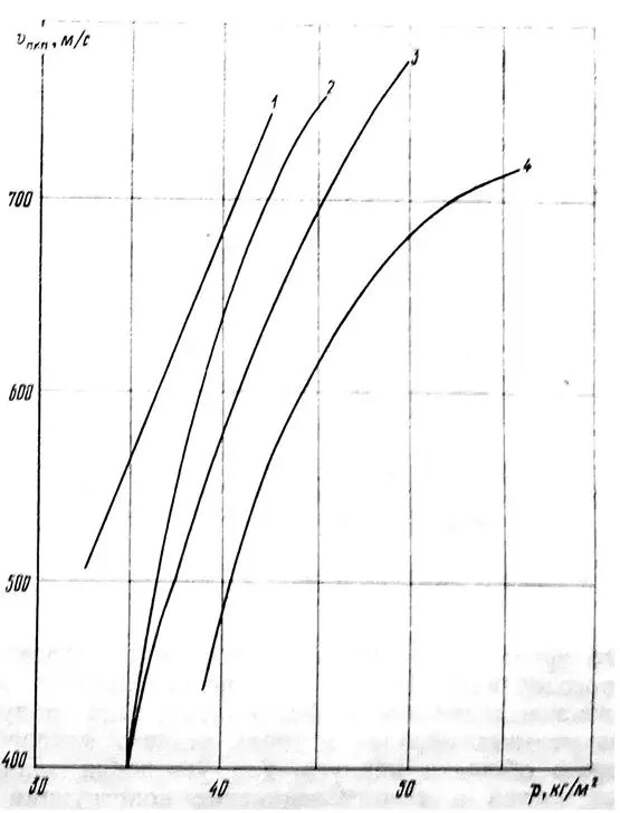
Рис. 1. Пулестойкость при обстреле пулей Б-32 калибра 7,62 мм (зависимость предела кондиционного поражения от поверхностной плотности р защиты) композитных броневых преград с опорным слоем из стеклопластика марки МПС и лицевым слоем из: 1 – атенита толщиной 8 мм; 2 – карбида кремния 9 мм; 3 – корунда 7 мм; 4 – керамики типа ГМТ 8 мм. Примечание: Vпкп по оси X — скорость пули при соударении с бронёй, при которой не наблюдается сквозных пробоин, проломов и прочего.
Матрица (рис. 2) представляет собой неразъемное жесткое основание, сваренное из профильного проката со съемными частями по бортам и в носовой части корпуса, с приспособлениями для снятия изделия после формования, для получения местных обводов в зонах резкого изменения формы обшивки корпуса, для установки закладных частей и т. п.
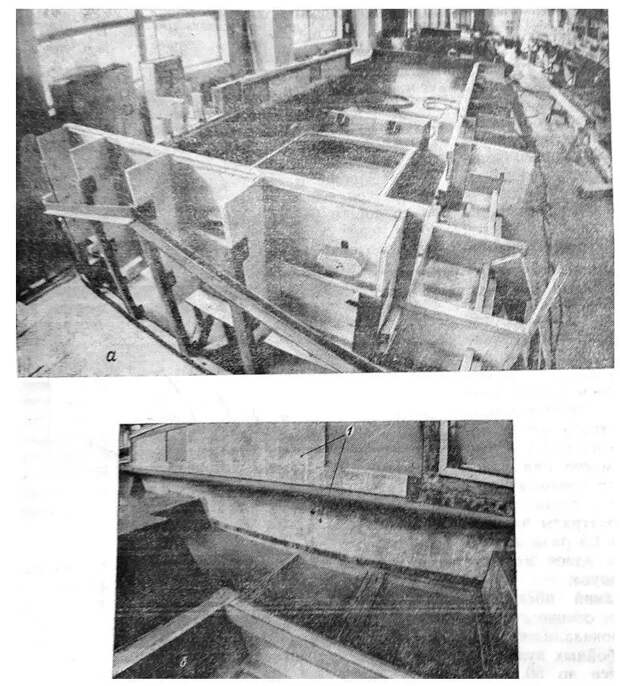
Рис. 2. Общий вид матрицы (а) и устанавливаемых в нее керамических блоков (б): 1 – верхний и нижний бортовые блоки
Соединение конструкций из стеклопластика и металла выполнено клеем марки К-153 или ЭПК по ОСТ 5.9767—79 без наполнителя. Для заформовки винтовых соединений в зонах, где специальные покрытия отсутствуют, использована паста, приготовленная из рубленой стеклоткани, эпоксидного связующего К-153 или ЭПК. Отдельные части корпуса, изготовленные формованием в матрице, сварены между собой. При матричном способе изготовления керамический наполнитель может быть размещен на необходимой глубине слоя стеклопластика, наружные поверхности корпуса машины отличаются высоким качеством. В зависимости от массы машины, типа устанавливаемого на ней оружия, скорости движения и динамических характеристик подвески могут применяться различные схемы корпуса, каждая из которых должна обеспечивать прочность и жесткость.
Опыт по использовании различных композитных материалов, накопленный к настоящему времени, позволяв предложить три основных варианта конструктивных схем корпусов для ВГМ легкой категории по массе.
Цельный пластмассовый корпус, представляющий собой несущую систему бескаркасного типа, в которой с помощью клеевых и резьбовых соединений устанавливаются опора башни, подмоторная рама, перегородки, устройства крепления подвески и др. Такой корпус может использоваться для легких небронированных машин, а также для легкобронированных машин с подвеской (например, гидропневматической), передающей корпусу небольшие нагрузки.
Комбинированный корпус (рис. 3, а) из пластмассы, но с металлическим днищем. Пластмассовая часть его и днище связаны переходным устройством с помощью клеевых и резьбовых соединений или сварки. Он может использоваться для ВГМ или колесных машин массой более 10 т.
Пластмассовый корпус, усиленный металлическим каркасом (рис. 3, б). Он может применяться для легких бронированных машин. Кроме метода контактного формования, могут применять и другие методы изготовления пластмассовых корпусов в зависимости от программы выпуска, требований к качеству материала и конструкции, возможностей обеспечения технологического процесса.
Методом контактного формования могут выполнены все три рассмотренные здесь конструктивные схемы корпуса. Однако он не обеспечивает стабильности механических свойств материала, весьма трудоемок и потому может применяться лишь при ограниченных программах выпуска и в опытно-конструкторских работах.
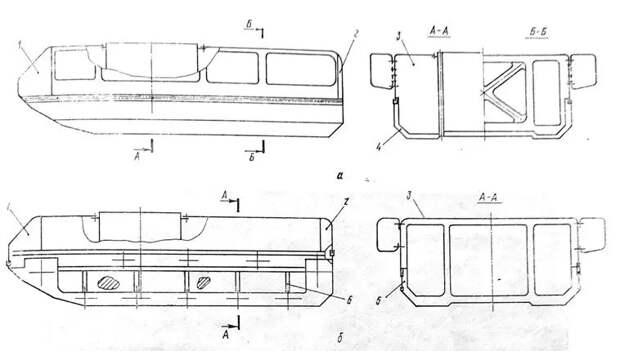
Рис. 3. Схемы корпусов комбинированного (а) и пластмассового, усиленного металлическим каркасом: 1 – верхняя часть корпуса (выполнена методом намотки); 2, 3 – носовая и кормовая детали корпуса (выполнены методом контактного формования или прессования); 4 – нижняя (металлическая) часть корпуса; 5 – соединительный узел; 6 – металлический каркас
Известным методом изготовления частей корпуса является прессование, дающее возможность получения 2-го и 3-го вариантов корпуса, но требующее уникального прессового оборудования.
Метод намотки также требует специального оборудования и сложной оснастки, не обеспечивая изготовление всех частей корпуса. Лобовые и кормовые детали корпуса в этом случае должны изготовляться либо методом прессования, либо контактным формованием. Метод намотки может быть применен для изготовления 1-го и 2-го вариантов конструктивных схем (см. рис. 3, а, б). Им изготовляется только средняя (трубообразная) часть корпуса, которая разрезается по диаметральной плоскости на две идентичные части; каждая из них становится верхней половиной корпуса. Остальные детали 2, 3 (см. рис. 3, б) выполняются методом контактного формования или прессованием.
Разработаны схемы корпусов стеклопластикового и комбинированного, изготовленных для ходового макета ВГМ (рис. 4). Верхняя часть последнего выполнена из стеклопластика методом контактного формования в матрице с наружным керамическим слоем. Соединение верхней 1 и нижней (металлической) 2 частей корпуса осуществляется с помощью специального переходного устройства 3.
В целях обеспечения заданной прочности и жесткости цельный пластмассовый корпус БМД при минимально возможной массе выполнен полностью из стеклопластика в виде несущей системы бескаркасного типа. Материал оболочки — стеклопластик холодного отверждения на основе стеклоткани Т11-ПВС-9 и полиэфирной смолы ПН-609-21М. В качестве заполнителя в поперечных балках применен пенопласт марки ПХЗ-1. Оболочка корпуса имеет толщину 15 мм, лобовые и передние бортовые детали — 30 мм, что отвечает требованиям по противопульной стойкости. Верхняя часть корпуса формовалась в матрице на двух деревянных пуансонах (верхнем и нижнем) по типовой технологии. Опора башни, подмоторная рама, перегородки и другие неразъемные элементы устанавливаются в корпус с помощью клеевых соединений.
Применение композитных материалов при изготовлении корпусов и башен легких машин позволяет дополнительно уменьшить заметность машины, вероятность поражения ракетами с головками самонаведения и минами, взводимыми магнитным полем, а также заброневую дозу проникающей радиации. При этом возможно повышение точности стрельбы за счет снижения уровня шума и вибраций.
К эксплуатационным преимуществам применения композитных материалов можно отнести:
1. Отсутствие необходимости в частой очистке и окраске элементов корпуса, а также уменьшение (либо полное исключение) работ, связанных с ликвидацией последствий коррозии;
2. Снижение вероятности появления трещин от ударов;
3. Упрощение ремонта в процессе эксплуатации; улучшение эргономических показателей (ниже уровень шума, вибраций, легче тепловой режим).
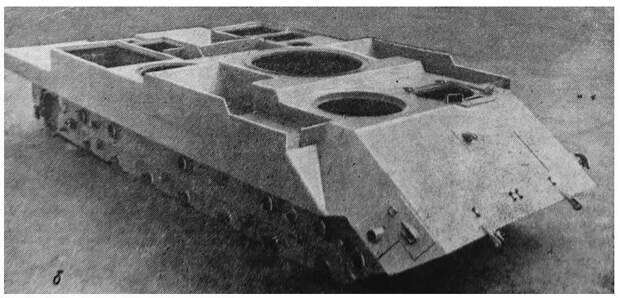
Рис. 4. Общий вид комбинированного корпуса для ходового макета ВГМ
Из-за перечисленных преимуществ выполнять корпус и башню из стеклопластика оказывается экономически более выгодным, чем из металла.
Технологические преимущества использования композитных материалов включают:
Значительное снижение энергозатрат;
Возможность изготовления корпусных конструкций практически любой формы с более высоким качеством поверхности и более низкой трудоемкостью, чем у конструкций из традиционных материалов;
Уменьшение трудоемкости (если, например, для изготовления металлического корпуса необходимы специальные приспособления, электро- и газосварочная аппаратура, штампы, прессы, высококвалифицированные рабочие и специалисты, то для изготовления пластмассового корпуса требуется лишь теплое помещение, оснастка и формовщики сравнительно низкой квалификации);
Использование более дешевых материалов (серийно выпускаемые керамические плиты на основе корунда стоят 9 тыс. руб. за 1 т; на один корпус расходуется 0,4 т таких плит).
К недостаткам композитных материалов следует отнести низкий модуль упругости, а также невысокую прочность соединения элементов конструкций между собой.
Использование композитных материалов для изготовления корпусов и башен основных танков весьма проблематично. На данном этапе развития танкостроения защита от бронебойных подкалиберных снарядов осуществляется в основном за счет стальной составляющей комбинированной брони. Однако возможно широкое использование композитных материалов в конструкциях корпусов и башен основных танков в качестве «упаковки» для керамического наполнителя, устанавливаемого в преграды, для изготовления навесных защитных модулей с керамикой. Они могут быть применены также в конструкциях крыши моторно-трансмиссионного отделения, лючков корпуса, стенок отсеков, кормовых деталей корпуса и башни.
В случае выноса некоторых элементов внутреннего оборудования танка на надгусеничные полки (например, аккумуляторных батарей, фильтровентиляционной установки, автономного энергоагрегата) последние могут быть надежно защищены от осколков снарядов и пуль экранами из композитных материалов.
Вывод. Использование композитных материалов для легких ВГМ позволит уменьшить их массу при сохранении заданного уровня броневой защиты или повысить уровень защиты при сохранении массы и обеспечит некоторое уменьшение вероятности поражения, а также улучшение эксплуатационных и производственно-технологических показателей машин.
Источник:
«Использование композитных материалов для лёгких ВГМ». А. В. Козлов, О, М. Лазебник, А. Ф. Мисюк, Б. И. Бобров. Вестник бронетанковой техники №4 за 1990 год.
Свежие комментарии